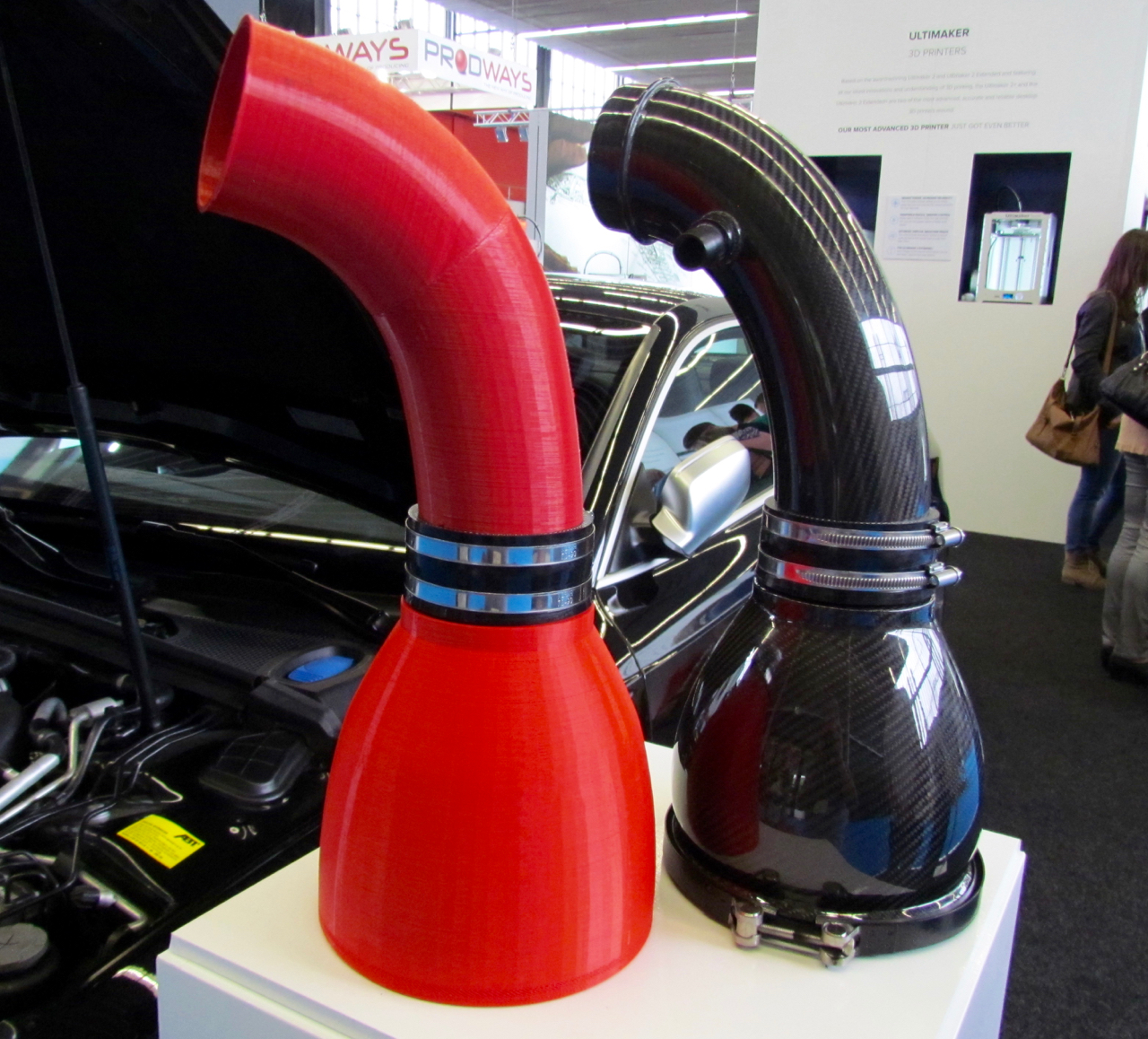
At the very beginning, Ultimaker was a group of guys who built a hobby 3D printer. Now, things are utterly changed.
The company has been undergoing a transformation towards more professional uses of the machines, and appears to be successful.
They’re not alone in transforming; the entire desktop 3D printing industry has been making the switch from DIY hobby / consumer applications to engineers, designers, educators and other professionals. The reason: cash! There’s a relatively limited number of consumers and hobbyists, who by the way are not the market with the most money, while there are much more vast numbers of professionals, who do indeed have money to spend on 3D printers.
And they’ll do so only if the machines can actually make their life better.
That’s what many leading 3D printer companies are now focusing on: demonstrating true value of their products within specific industries. Ultimaker is no different in this regard, and has recently shown several interesting business applications.
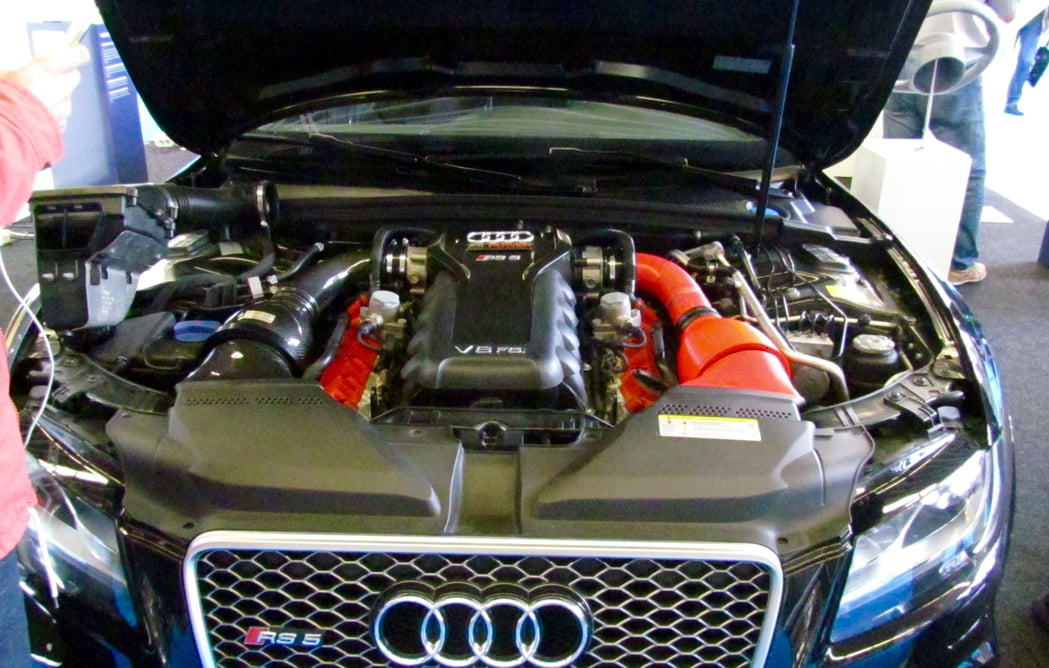
One very interesting demonstration they’ve portrayed is a kind of “mobile automobile part prototyping workstation”. They worked with Eventuri, a company dedicated to producing high performance aftermarket air intakes for notable car models. You can, for example, buy an upgrade kit from their for your newly-purchased Lamborghini that provides more power – and even better noise!
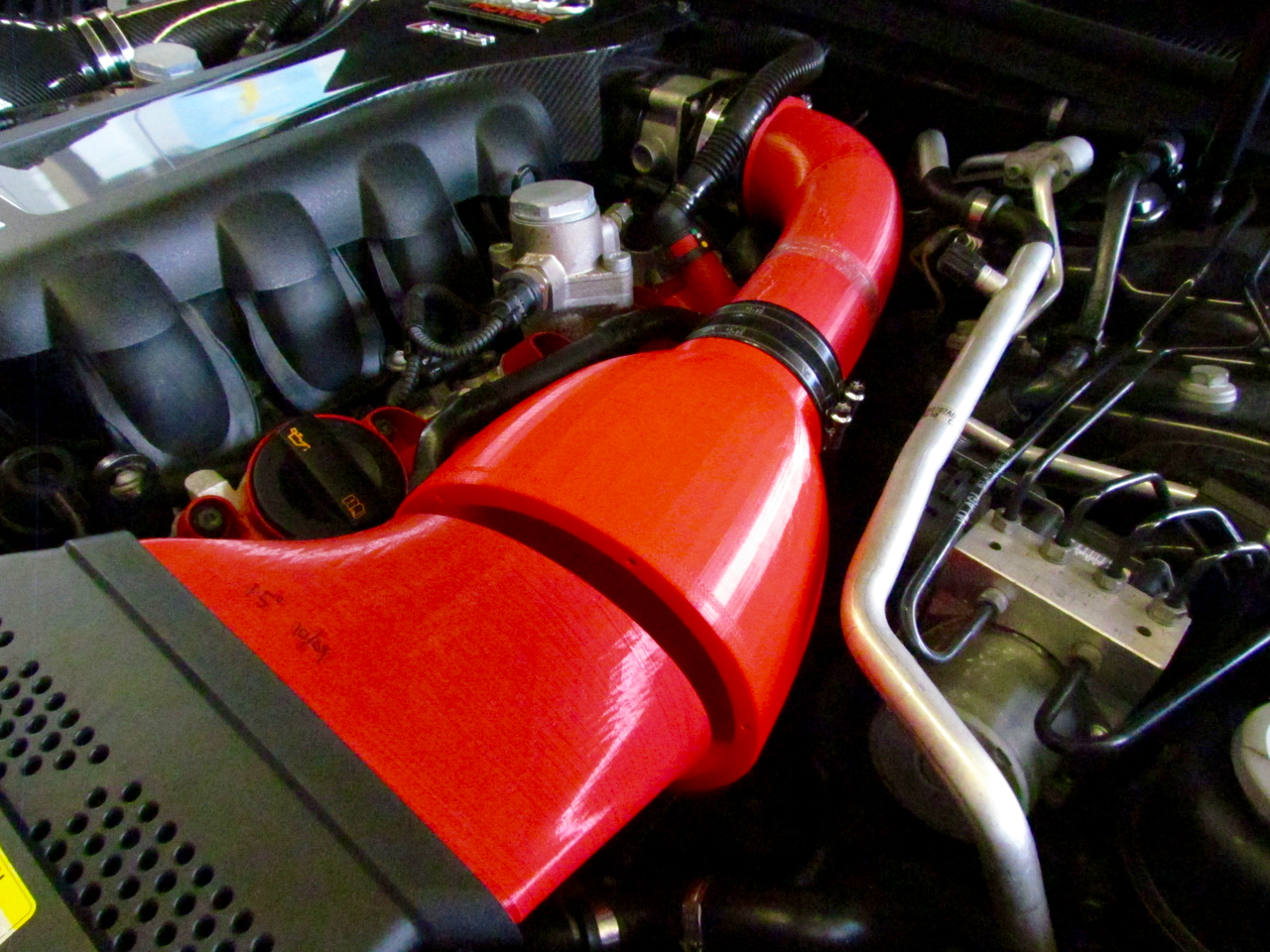
Their problem is that they have access to the rare automobiles for only a limited time. Their solution: take a (mostly) portable Ultimaker 3D printer onsite to the vehicle. Make measurements of the air intake; Modify the design; 3D print a prototype onsite; Test for fit; Repeat as required until a final correct design is achieved.
This approach shortcuts the usual method of sending information and parts back and forth between design studio and worksite. It’s a pretty good idea and apparently worked very well in this instance.
That’s one of several unusual business applications being featured by Ultimaker in their journey towards a new company focus.
Via Ultimaker