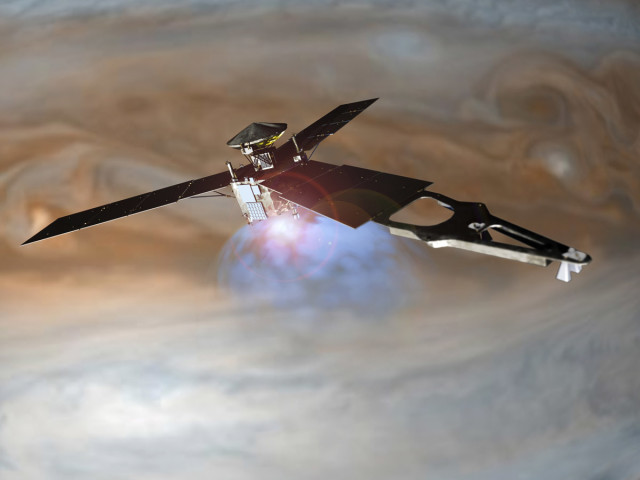
After a five-year journey, NASA’s Juno spacecraft has arrived at its destination: the orbit of Jupiter, where it will collect data about the solar system’s largest planet.
The Juno mission, managed by NASA’s Jet Propulsion Laboratory (JPL), has accomplished a number of firsts—including the first planetary spacecraft to make use of 3D-printed components.
Juno was constructed in part by defense giant Lockheed Martin, which chose to use 3D printing to produce about a dozen waveguide titanium brackets for the spacecraft. To fabricate the parts, Lockheed used an electron beam melting machine from Arcam, which uses an electron beam to melt titanium powder one layer at a time before a knife blade moves subsequent layers of powder onto the bed.
Stacking the brackets within the system’s 8 in x 8 in x 14 in build envelope enables cost-efficient batch production. By 3D printing the brackets, the company was able to reduce the cost and manufacturing time for the components by about 50 percent.
On Earth, Lockheed first conducted confidence testing to ensure that the parts would perform as expected before the spacecraft was ultimately launched aboard the Atlas V 551 rocket on Aug. 5, 2011. Now that Juno has survived the 1.76-billion-mile journey to Jupiter, entering the planet’s orbit on Jul. 4, 2016, the brackets are being put through the ultimate test as they orbit around the gas giant.
Read more at ENGINEERING.com