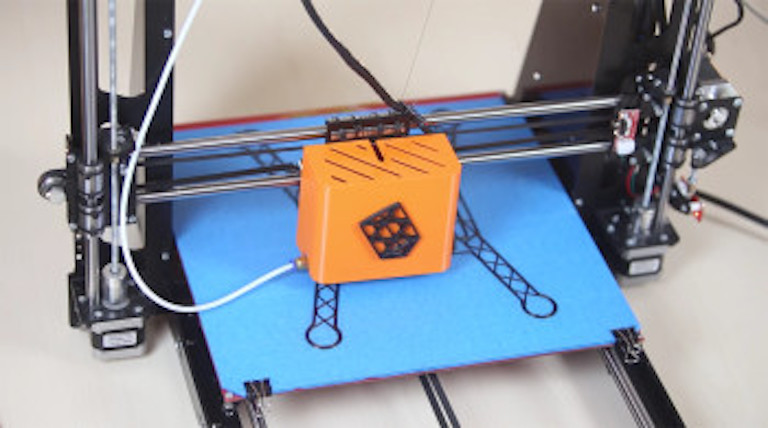
When the first 3D printer in space landed at the International Space Station (ISS), it could 3D print with ABS, the plastic found in LEGO bricks.
Made In Space subsequently improved upon its Zero-G 3D printer with what the company calls the Additive Manufacturing Facility, a commercial 3D printer that can print in high-density polyethylene and polyetherimide-polycarbonate composite, in addition to ABS.
Now that the first commercial 3D printer is installed aboard the ISS, the next moves for space additive manufacturing will involve upgrading those 3D printing capabilities even further. A team from Russia plans to do just that by sending a 3D printer to the ISS that can fabricate carbon fiber composites for rigid, durable microsatellites.
The project will see two companies from the Skolkovo tech park, Sputnix and Anisoprint, team up with Moscow Polytechnic University to develop a 3D printer capable of blending traditional thermoplastics with continuous carbon fiber reinforcement to produce parts that can survive the depths of space.
The base technology was developed by Anisoprint, which has created a printer that works by feeding continuous strands of carbon fiber into a thermoplastic object as it is being printed. This results in parts with 10 times the rigidity of thermoplastic parts, according to the Russian team. If this sounds familiar, that’s because Markforged employs a similar process to reinforce nylon objects with carbon fiber, Kevlar and fiberglass.
Together with microsatellite manufacturer Sputnix, Anisoprint will be modifying its 3D printer for use in microgravity this summer. This will involve taking into account the safety requirements of the Russian sector of the ISS and anticipating the effects of printing without gravity. To understand how 3D-printed parts will survive in space, the partners will subject them to a thermal environment simulation chamber and a vibro-bench.
Fyodor Antonov, director of Anisoprint, explained the advantages of its technology for space manufacturing: “The American printer uses ABS plastic and is most suited for printing supplementary instruments and prototypes of devices. To make actual construction elements for space technology, more research is required. The fundamental difference between our Russian invention and the American one is that our printer prints with composites—not just plastic, but continuous carbon fiber-reinforced plastic. We’d like to use our device to print—right up there in orbit—parts of satellites made out of carbon fiber-reinforced plastic, practically the same kind used on Earth to make the main body of large satellites, solar battery panels, antenna reflectors and all sorts of other elements of spacecraft.”
Once the printer is complete, the team will prep for sending the printer to the ISS, where it will begin printing test items, such as solar battery panels, antennae components and fixtures. The ultimate test, however, will be to 3D print whole devices, such as CubeSats, to be outfitted with electronics already aboard the ISS and send them out into space.
Read more at ENGINEERING.com