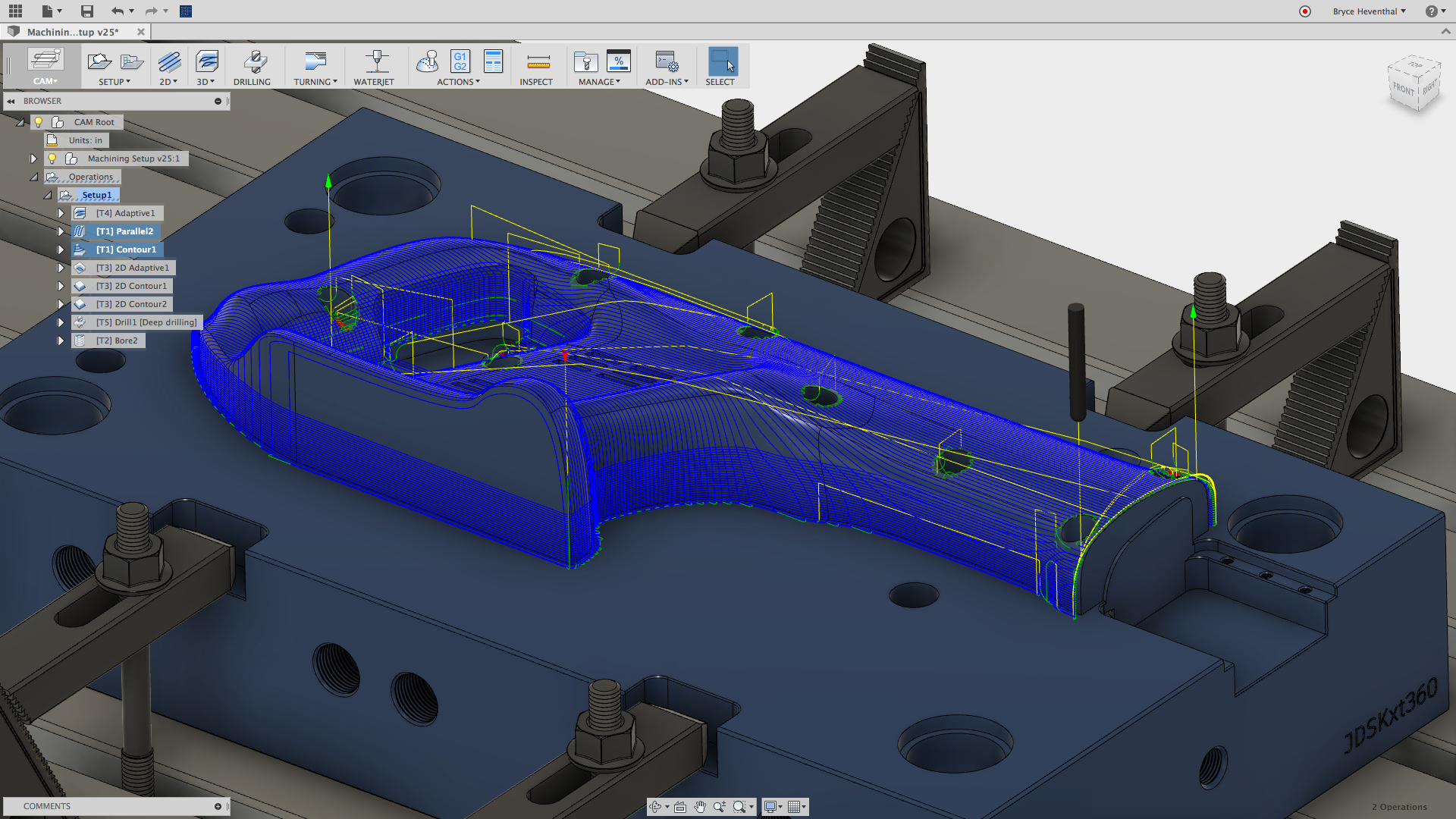
The O’Jays. Remember those guys? Probably not, but I guarantee you’ve heard their most popular song, For the Love of Money.
Two chords and a repetitive five-word phrase later, and you’ve got a song stuck in your head for longer than you want. Those could easily be five reasons integrated CAM matters to engineers. But alas, we know engineers are not that superficial. So, in our final foray into Fusion 360 features, we’re going to look at something you shouldn’t overlook–its integrated CAM functionality.
But rather than talk waaaaay out of my proficiency about CAM features like toolpath setup, tool libraries, roughing & finishing, and all things CAM as though I’m Machine Shop Billy flicking cutting oil in your eye, I’ll take a slightly different path. I’d like to talk about the steps to understanding CAM in Fusion 360, but in the context of what it does to help (crank the reverb) ENGINEERING TEAMS.
Before You Even Start Modeling
When first working in a manufacturing environment, I asked myself, what manufacturing processes do I need to know? And, why do I need to know them? Fortunately, Shop Manager Mike heard me and broke it down for me in simple terms and foul language with three things to think about before slapping model geometry together.
Materials – Mike: “You’ve got to know what’s available and what’s commonly used, you stupid #$*%ing engineer. Think of stock size, @$$#0&%, and ways to reduce waste!”
Tools – Mike: “If I have to change that tool more than twice, I’ll kill you *!$#&%. Even a basic part is going to have, at the very least, two setups. I smoke with this hand and this one only has three fingers!”
Rework – Mike: “If I have to redo any of your $#!%, I will beat you with that #%&(@! useless 20-sheet drawing. Then you’ll know how much someone can bleed on a piece of $%&*@in’ paper! $H%$*#!”
I’m so thankful for Mike and the time he took to help me understand the basics of the manufacturing process. True enough, these are things many designers and engineers are not privy to until they’re in the thick of it. Right up front, get to know the process. What is and isn’t possible. What processes make the transition from engineering to manufacturing go more smoothly. This way, before something is handed off to the shop, the likelihood that it can actually be manufactured will be more than just a guess.
This, of course, is where integrated CAM comes in. I’m looking at this, not from becoming an overnight CNC success, but to better understand HOW toolpaths are created and how it can be an aide in the product dev process. At the very least it provides insight. At most, it saves time, material and rework, which helps save… cue the O’Jays. So let’s take a step-by-step look at features I wish I had along the way, features I think will become increasingly important to engineers and designers, while keeping Mike’s gentle words in the back of our head.
Step 1. Creating the Setup
Suddenly you have a final part. Hours spent modeling. It’s perfect. You considered size and stock material availability, even the position it was modeled it in. But let’s not get too far ahead. The first feature we can use in setting up a toolpath is determining a Work Coordinate System (WCS). Even if you didn’t model it in the correct position or know for how the part is going to be machined, The Fusion 360 CAM setup can help set the WCS with the quick selection of an edge to properly orienting the model for the machine.
Step 2. Roughing
A quick definition here – Roughing a part is removing as much material as possible in the shortest amount of time as possible. Fusion 360 does this with the Adaptive Clearing feature. We touched on this in our first article, but if you don’t know what Adaptive Clearing is like from a machinist point of view, read this article. To simplify it for myself, I look at it like this (tell me if I’m wrong): Adaptive Clearing utilizes an adaptive algorithm that applies a constant tool load to the clearing path so any overloading on the machine tool is prevented, ensuring uniform wear across the tool, thus increasing the life of the tool. This is where I would make the recommendation to involve the machinist in what you are doing. Get his or her feedback (and confidence) about how you’re approaching the design, not to do what they’re doing, but to make sure it can be done and in the long-run, reduce their work or re-work.
Step 3. Finishing
Read more at SolidSmack.com