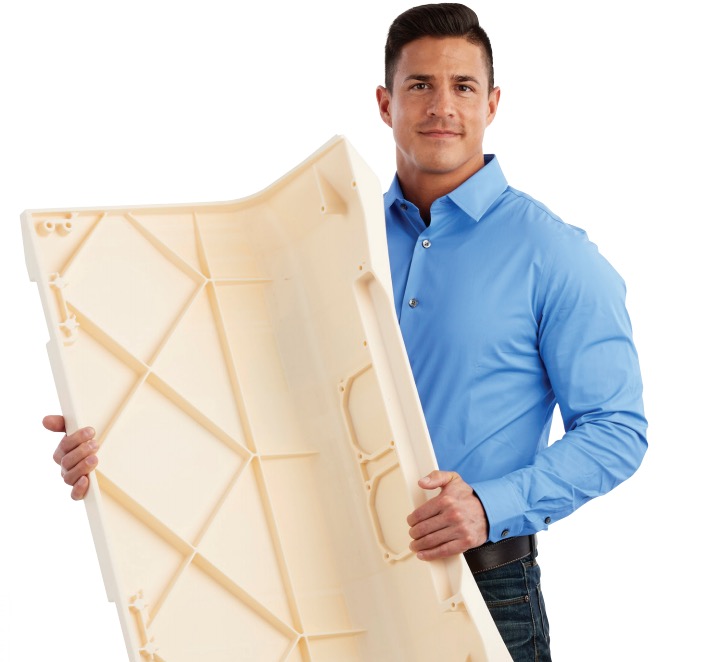
There seems to be an interesting theme emerging from Stratasys these days, and it’s not simply announcing hardware.
One of the most interesting aspects of their recent announcement of the multicolor, multimaterial J750 machine is that it attacked the business workflow OUTSIDE of the machine. As I explained in a previous post, the new machine profoundly changes how products are developed by enabling much more rapid product testing workflows.
Now Stratasys recently made another announcement regarding several of their products. It’s by no means as splashy as the J750 announcement, but certainly follows the same themes of simplifying customer workflows. Here’s what they announced:
They’ve produced a new type of dissolvable support material, ST-130, which differs from it’s predecessor in one very critical way: it has a far higher melt temperature. This enables their 3D printers to be used in an entirely new way: instead of printing finished plastic objects, instead standalone dissolvable objects are printed.
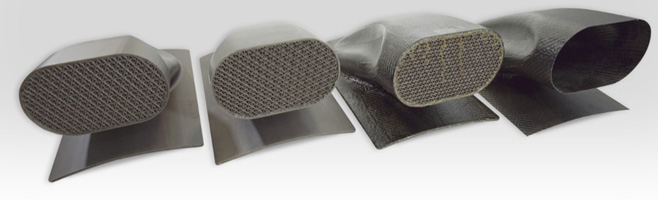
Wait, why would you want to print something that’s entirely dissolvable? It’s because the intention is to print dissolvable molds for composite lay-up work. In other words, when composite materials are cured in high-temperature autoclaves, the mold printed in ST-130 survives! It can then be dissolved away in the usual manner. This opens up an entirely new type of 3D printing application for Stratasys, as now more complex composite objects can be made with such molds.
The second piece announced was an “acceleration kit” for certain Fortus FDM printers. It’s a bit hard to find, but I finally realized what they were doing here: it’s a specialized nozzle replacement that provides a lot more plastic flow. Normally, Fortus “tips” are typically around 0.4mm in diameter, similar to desktop machines. They have a few variations on that size for slightly different resolutions.
However, the new kit provides a 1.0mm nozzle, significantly increasing the plastic flow. This means you can print larger objects much faster, and they claim you can save as much as 61% on the print time. Here’s an example:
Using a standard T20 Tip (13 slice) 160 hours
Using the new T40A Tip (20 slice) 63 hours
Ergo Time Savings 97 hours (61%)
This is very significant for anyone printing large objects on a Fortus.
But again, they’re directly addressing the needs of their clients, who have no doubt been asking for such improvements. They’re simplifying the workflow of manufacturers, and I expect they’ll be announcing more on this theme in the future.