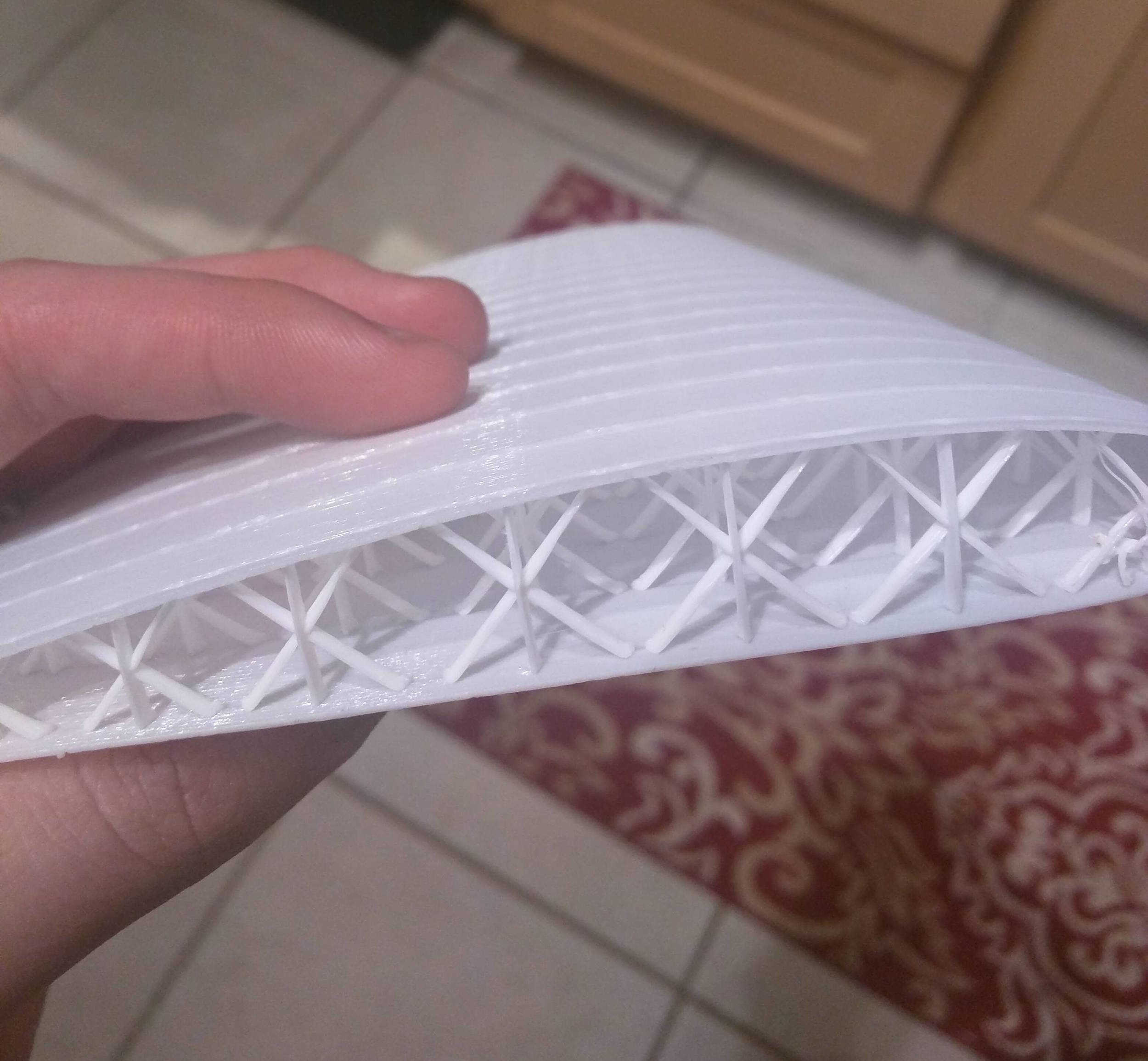
Highly complex 3D printed structures are being explored by large corporations for unique products, but can this be done by those with lesser equipment? Apparently so!
Reddit user JSchall2 has been experimenting with a python script that generates GCODE for an airfoil with relatively complex inner supports. Evidently the script permits you to configure a number of key airfoil parameters to enable creation of a suitable wing shape.
The lengthy discussion on Reddit suggests that the wing design may not be optimal according to actual aerospace engineers, the weight may be more than needed, the supports may not be the right style, the generator could be constructed using other software, the outer skin should be smoothed, perhaps by using ABS and acetone, and other recommendations for improvement.
However, those are not the points I’d like to make here.
The point is that we have an individual with a set of inexpensive equipment and software, who’s able to experiment in this area: developing complex functional structures that would otherwise be challenging to produce.
This is the same approach being used by NASA and aerospace companies to develop lightweight, reliable, highly functional parts to replace bulky equivalents made using conventional techniques. NASA, for example, has been able to produce a rocket engine that has significantly fewer components. Their design reduced the weight due to losing the need for connecting hardware and increased reliability because there are fewer seams to be compromised.
Similarly, architects and designers have been developing unique construction components that again save weight and material, while still providing more than adequate strength characteristics.
One reason why this type of experiment has remained in the realm of industry and high-end research is that there isn’t a lot of easy-to-use software to assist in generating the highly complex structures required.
But perhaps with the efforts of JSchall2 and others, such software can gradually be developed and deployed to the public for more widespread use – and experimentation.
When a great deal more people are experimenting – and likely in areas not yet explored by industry – we could see many interesting developments, and if we’re lucky, a few new industries.