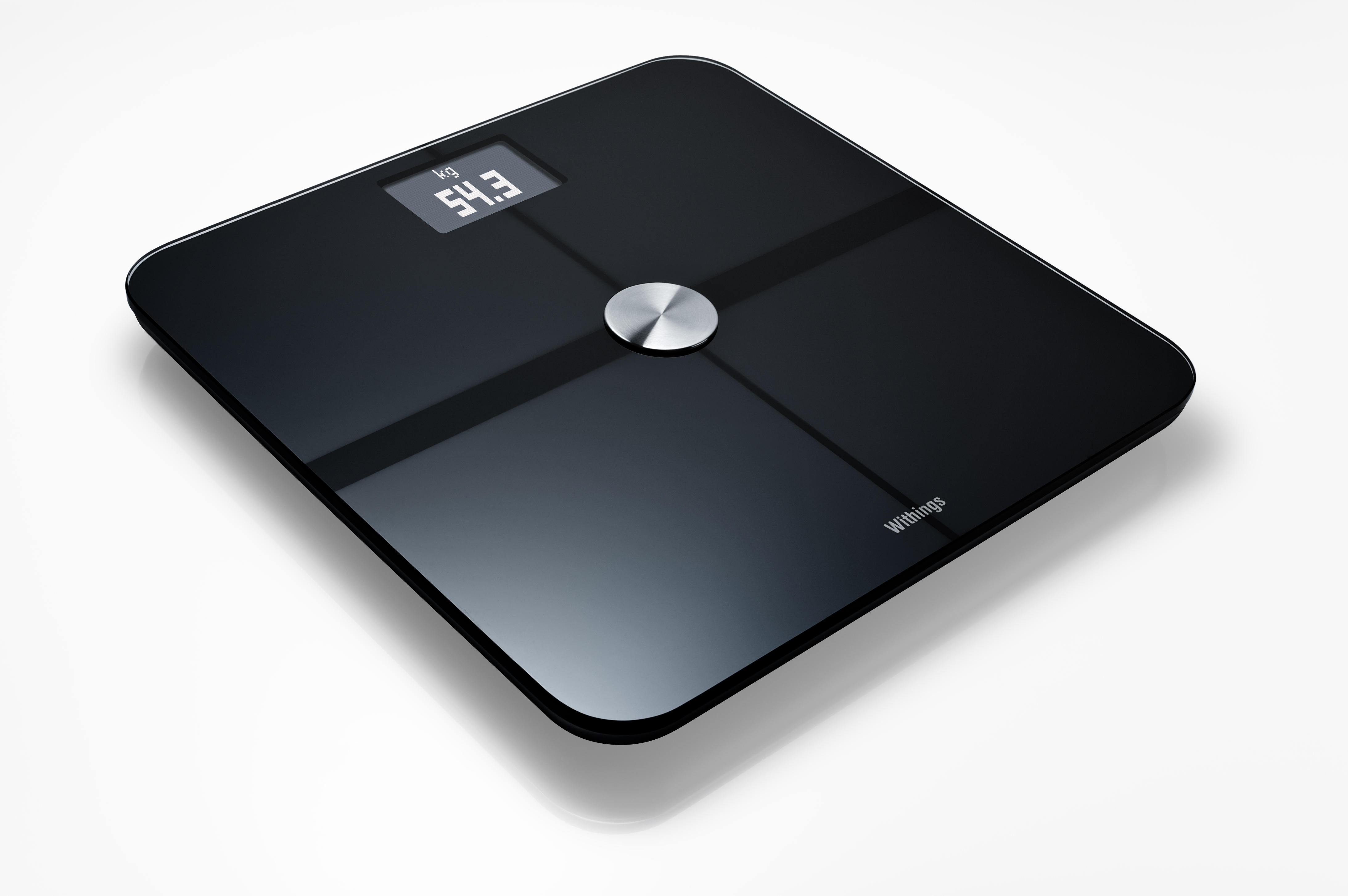
For those accustomed to digital manufacturing using 3D printing, it’s becoming hard to imagine how companies designed products in the past. Today’s leading companies use a digital process to create their offerings, and that’s precisely what Withings did to develop their latest smart scale.
Withings, if you don’t know, produce an amazing personal weight scale that not only provides weight, but it also computes body mass index, fat percentages and more. Then it saves this data automatically online through a WiFi connection to a cloud service, where you can check the stats from the web or app.
Their latest offering, the Smart Body Analyzer, came about through 3D printing, but not exactly as they had planned. To produce first few units of the new scale they had made arrangements with a conventional mold maker to produce the molds for three plastic holders for new air sensors. Suddenly the mold maker had a delay, causing Withing’s ship schedule to slip significantly.
Withings’ solution: Contact 3D print service Sculpteo and have them rapidly produce the first 100 sets of parts to permit Withings to launch the new product on schedule. Sculpteo was able to not only print the batch, but they also quickly developed a unique process to clean the parts sufficient for use in the product. In the image above you can see the 3D printed part (left) and a traditional injection molded part on the right. It’s not quite the same quality – but it is more than sufficient to perform the required function inside the scale.
They say 3D printing is a niche technology, but it doesn’t have to be. You need only be creative. In fact, we’ve barely explored the possibilities.