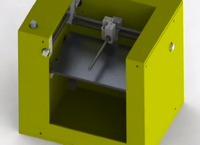
- The design is even simpler than other 3D printer designs. For example, rather than using belts and bearings, they’re using drive screws. These design simplifications lead to much less cost
- The build envelope is actually a heated chamber! Motors and electronics are kept outside, meaning they do not need to be beefed up to handle the heat of the chamber. Again, lots of benefit at a low construction cost
- Volume priced components, as they’re hoping to build a lot of these units
- Although not part of the printer itself, MakiBox will sell ABS plastic at the incredibly low price of US$20 per Kg (about USD$9 per pound), the lowest we’ve seen. They’re also introducing a new filament size: 1mm
We love innovation and it appears that MakiBox is doing quite a bit of innovation. We’re hoping they’re successful – and they will be if you contribute to their project at the link below.
I agree additional materials is what will make platforms like this more usable. Definitely planning on figuring out how to get wax output for castings. I can see this making a semi-manual process where the printing helps save time for artists.
I agree additional materials is what will make platforms like this more usable. Definitely planning on figuring out how to get wax output for castings. I can see this making a semi-manual process where the printing helps save time for artists.
I would love to see a device like this that does wax printing, since that can be used to create investment molds for metal or resin casting.
I would love to see a device like this that does wax printing, since that can be used to create investment molds for metal or resin casting.