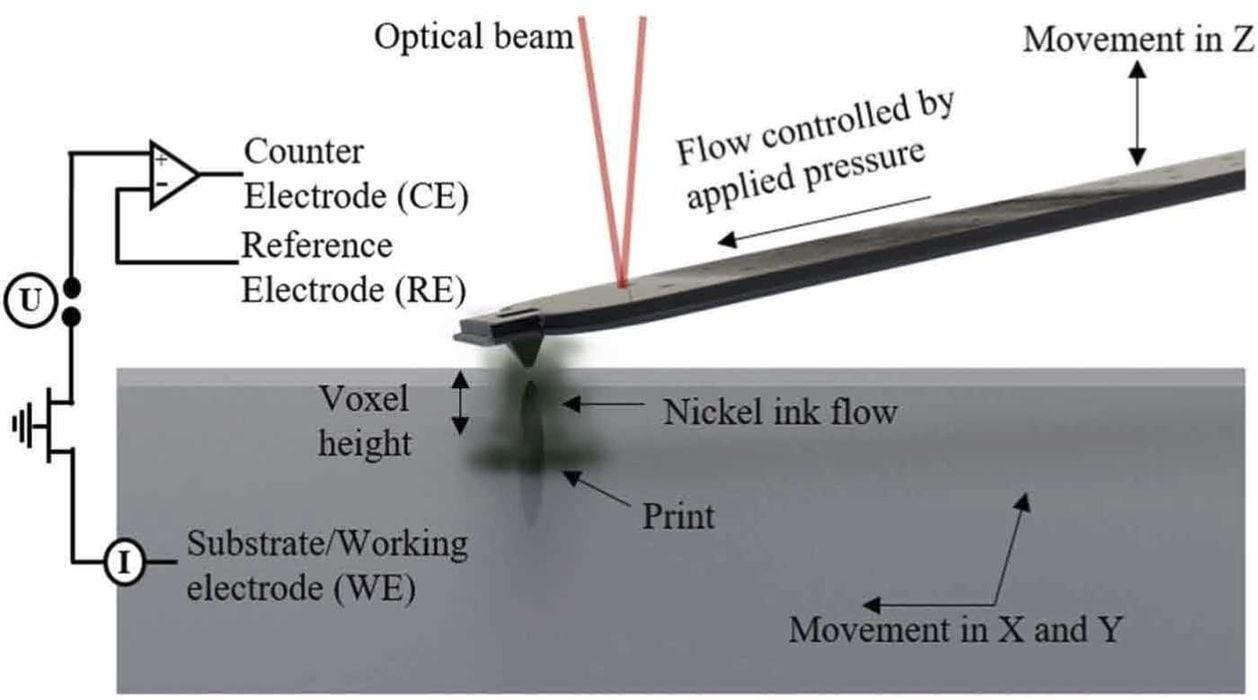
A new study has developed a method of 3D micro printing of nickel material at room temperature.
The recent study entitled, “From 2D to 3D Electrochemical Microfabrication of Nickel Architectures at Room Temperature: Synthesis and Characterization of Microstructure and Mechanical Properties” explores a new way to perform microprinting of metals. The research explored the development and characterization of nickel (Ni) microstructures using an innovative electrochemical 3D microprinting technique, which operates at room temperatures.
Why Nickel?
Traditional 3D microprinting methods typically use noble metals like copper, gold, or platinum due to their favorable standard reduction potentials. However, these metals fall short in mechanical strength. Nickel, on the other hand, boasts superior mechanical properties but poses a significant challenge for 3D printing. Its negative standard reduction potential leads to hydrogen evolution and unstable printing conditions.
The study attempted to overcome these challenges by developing a stable, high-speed electrochemical 3D printing process for Ni micro-architectures at room temperature. Additionally, the research sought to investigate and compare the mechanical properties and microstructures of 3D-printed Ni structures with 2D deposited films.
Materials and Methods
The researchers formulated new Ni-ink solutions and supporting electrolytes, evaluating them using linear sweep voltammetry and 2D electrodeposition. The optimal Ni-ink solution contained nickel(II) sulfamate tetrahydrate, boric acid, sodium dodecyl sulfate (SDS), and sodium sulfate. The supporting electrolyte was designed to minimize hydrogen evolution by incorporating sulfamic acid, sodium sulfate, boric acid, and SDS.
Using a CERES printer system from Exaddon AG, the process involved dispensing Ni-ink through a hollow AFM cantilever onto a substrate. Parameters like potential, printing speed, and electrolyte composition were fine-tuned by the researchers to achieve stable printing at high speeds.
Print Results
The team achieved a remarkable printing speed of 61 nm/s for Ni. That may seem extraordinarily slow when compared to desktop 3D printers, but itās a 45% increase over previous experiments. Remember, weāre printing very tiny objects with this technology.
The 3D printed Ni pillars exhibited a heterogeneous nanostructure, with grain sizes ranging from 13 nm at the center to 27 nm at the perimeter. The texture of these pillars was comparable to 2D deposited films.
Compression tests on the micropillars revealed a high compressive yield strength, which was only slightly lower than with 2D deposited films.
This study successfully demonstrates the feasibility of room-temperature electrochemical 3D printing of Ni with high mechanical strength and improved printing speed. The new electrolyte formulations, coupled with fine-tuned printing parameters, open a path for fabricating complex and mechanically resilient 3D microstructures. Potential applications span MEMS sensors, actuators, and other devices requiring high mechanical robustness.
By expanding the capabilities of electrochemical 3D printing, this research opens up new possibilities for the direct fabrication of tiny metal parts with superior mechanical properties, extending the range of applications for 3D printed micro-components. Iām also wondering if other metals could be used in a similar process.
Via Science Direct (Hat tip to Benjamin)