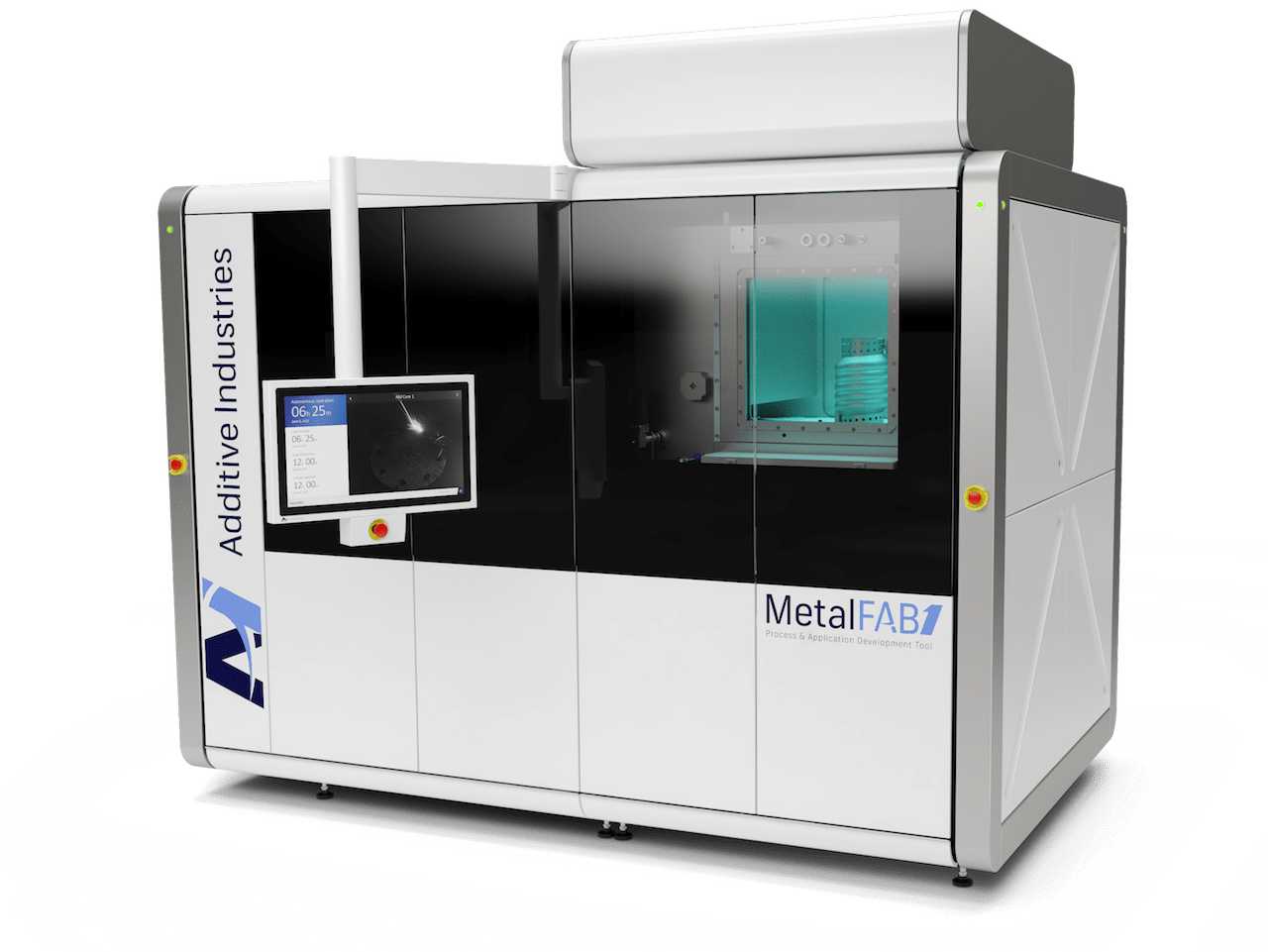
Eindhoven-based Additive Industries produces one of the physically largest 3D metal printing systems, but now they have a smaller version as well.
The company introduced the “MetalFAB1 Process & Application Development Tool” at Additive World this week. The new machine holds the exact same build volume as its much larger sibling, the MetalFAB1.
The new machine’s name is a bit unique and gives away the purpose of the machine. This is not simply a “mini” version of the original MetalFAB1, if you could use that word on such a large machine. No, it’s specifically for developing a suitable process for use on the larger machine. That, and general prototyping.
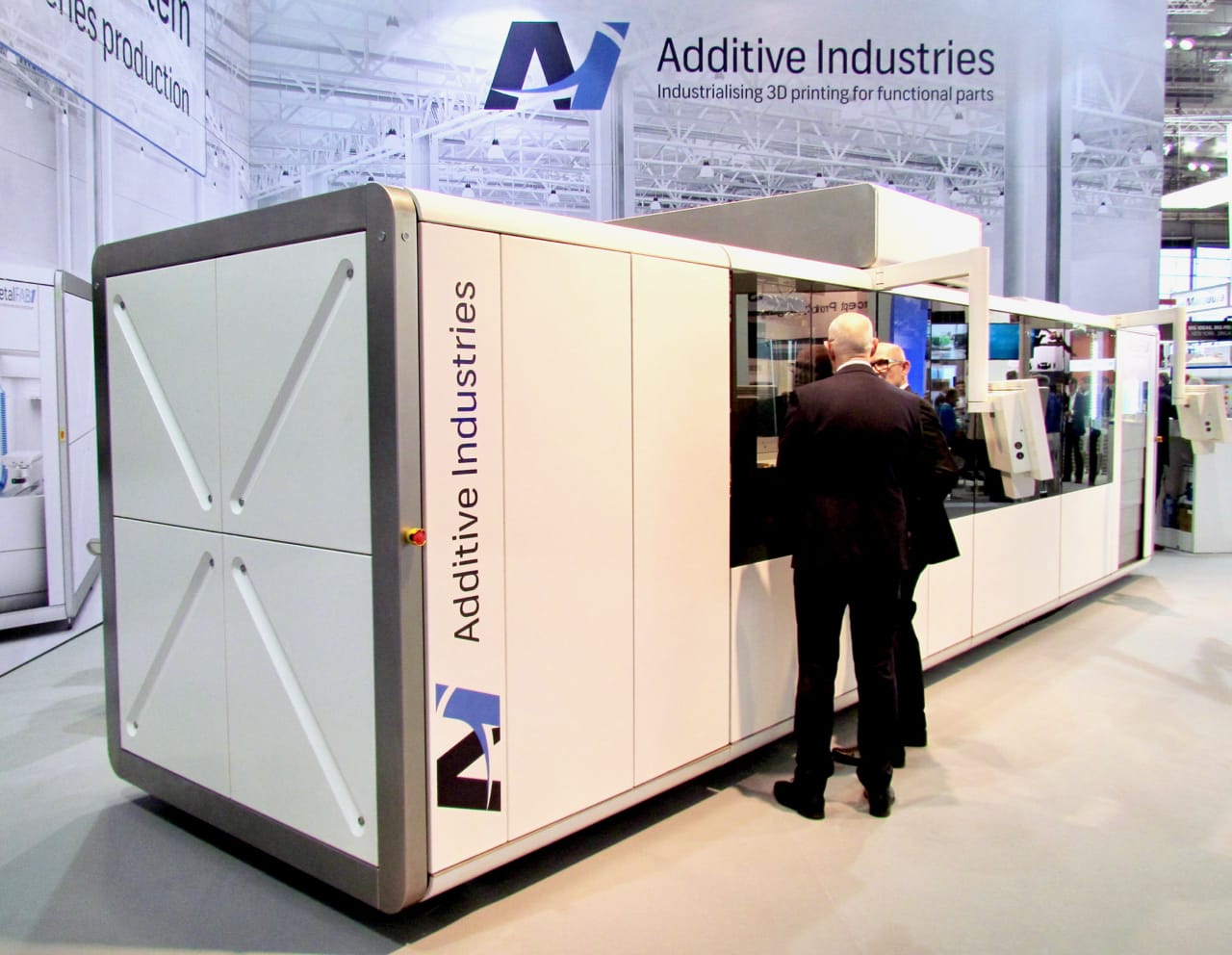
This falls squarely into the same approach Additive Industries took with the development of MetalFAB1: examine what the customer needs and build a system to match. That’s what the MetalFAB1 does: it is more than just a 3D metal printer. The system includes other modules that perform other required tasks such as post processing. By acquiring such a system, a manufacturer would have most of what they need to get into 3D metal printing.
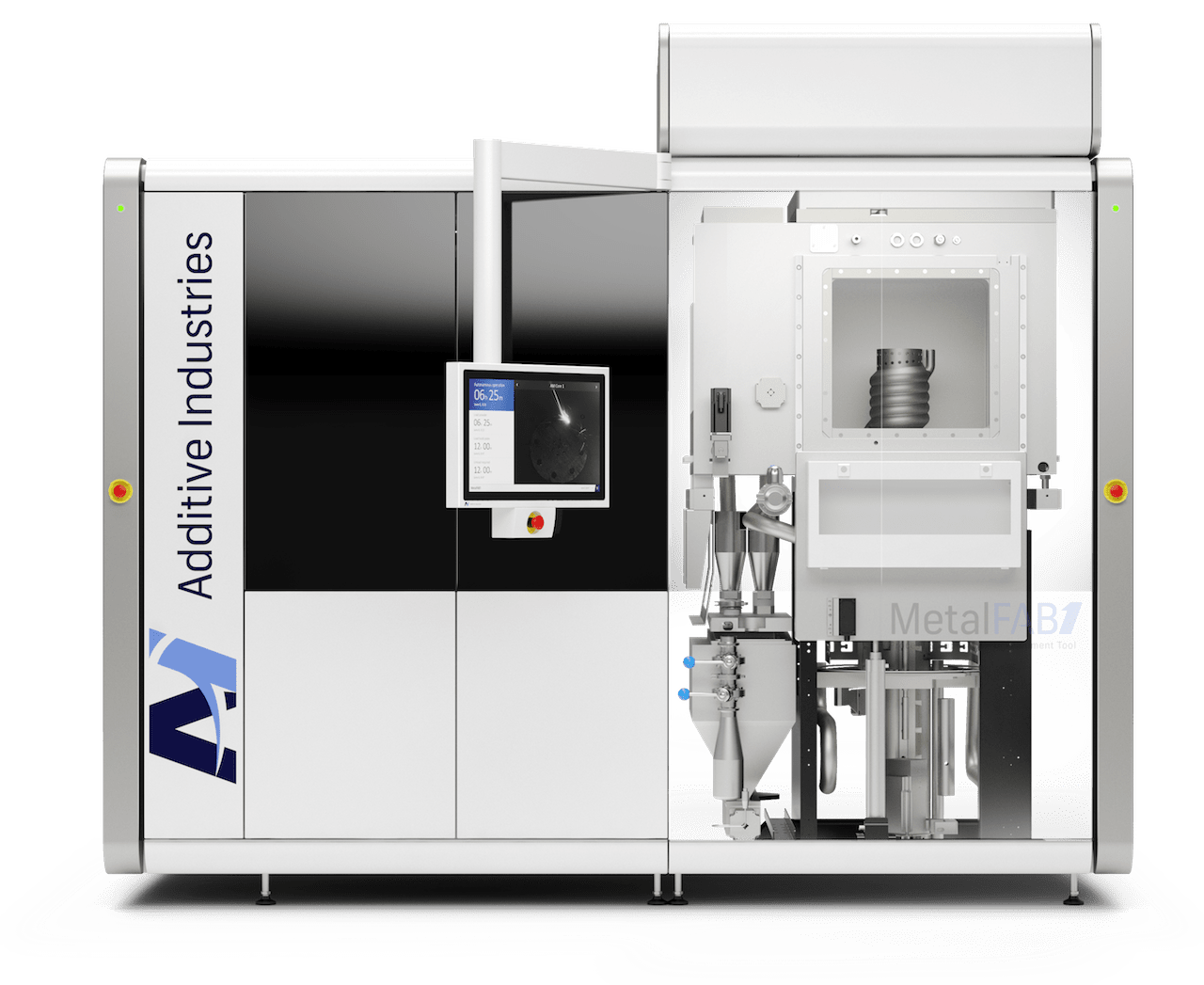
But then there’s the question of how best to operate the system given a particular manufacturing job. That’s where the new Process & Application Tool comes in: it can be used to iteratively develop a comprehensive production process that can later be deployed on the big machine.
The reason for doing the development on a second machine is simply efficiency: a big machine would presumably be busy producing other parts for previous projects and you wouldn’t want to interrupt its production for development. By investing in a second development machine, you could keep your MetalFAB1 running longer producing revenue-generating parts.
It’s a great idea and demonstrates how Additive Industries understands the issues of manufacturers.
I don’t have pricing on this new unit, but Additive Industries explains that it has a “competitive price point” and “compact footprint”, but I am certain they can help you with that.